A szalonban gyönyörködve, a családdal utazva a legritkább esetben gondolunk bele, milyen hosszú, összetett folyamat vezet el odáig, hogy átvehessük új autónk kulcsait. A Daciák például három különálló, ám egymással szorosan együttműködő helyszínen válnak tervből valósággá – ezeket járjuk most végig.
Az elmúlt években valami teljesen váratlan – bár visszatekintve teljességgel logikus – fordulat állt be az európai autópiacon. A Dacia, amely éveken át számított titkos megoldásnak azok számára, akik sallangoktól mentes, megbízható, kivételes ár-érték arányú autót szerettek volna vásárolni, hirtelen kilépett a reflektorfénybe. Az új generációs modellek feszes, sportos, divatos formavilága, a vadonatúj járműkoncepciók megjelenése, majd az átfogó arculatváltás lépésenként egyre magasabbra pozicionálta a márkát, amely így már nemcsak kedvező árainak, hanem szolgáltatásainak is köszönheti, hogy gyártmányai Európa-szerte a magánvásárlók kedvencei közé tartoznak. A nemzetközi sikerek láttán immár túlzás nélkül jelenthetjük ki, hogy a Dacia világszínvonalú autókat gyárt.
Az ehhez szükséges fejlesztési és gyártási infrastruktúrát három, egymáshoz viszonylag közel fekvő helyszínen biztosítja a márka. Ezek működése kísértetiesen emlékeztet a Dacia típusaira: bár mindegyik létesítmény ultramodern technológiai megoldásokat alkalmaz, azokat soha nem öncélúan vetik be. Ellenkezőleg: a gyakorlatias, józan célok elérését szolgálják.
A folyamat a Dacia Business Centerben indul, ahol több tucat, korábban külön helyszíneken található funkciók találkoznak egy tető alatt. A bukaresti irodaközpont helyszínét úgy választották meg, hogy az tömegközlekedéssel tökéletesen megközelíthető legyen. Ma még kevés autógyártóra jellemző ez a progresszív szemlélet, pedig pont ez jelenti a márka biztos jövőjét, hiszen napjainkban a fiatal mérnökök és formatervezők előszeretettel választják a környezettudatos, pénztárcabarát közösségi közlekedési lehetőségeket a belvárosi autózás kilátástalansága helyett.
A folyamat a Dacia Business Centerben indul, ahol több tucat, korábban külön helyszíneken található funkciók találkoznak egy tető alatt. A bukaresti irodaközpont helyszínét úgy választották meg, hogy az tömegközlekedéssel tökéletesen megközelíthető legyen. Ma még kevés autógyártóra jellemző ez a progresszív szemlélet, pedig pont ez jelenti a márka biztos jövőjét, hiszen napjainkban a fiatal mérnökök és formatervezők előszeretettel választják a környezettudatos, pénztárcabarát közösségi közlekedési lehetőségeket a belvárosi autózás kilátástalansága helyett.
A Dacia számára kulcsfontosságú a fiatal szürkeállomány: „A rövidebb szakmai tapasztalatukat bőségesen ellensúlyozza, hogy rengeteget forognak kortársaik körében, gyakran és örömmel kirándulnak, és otthonosan mozognak a közösségi médiumok világában, ezért naprakészen ismerik a célközönség értékrendjét, céljai és vágyait” – árulja el nem szokványos toborzási stratégiáját Yohan Ory, a Dacia Design Center igazgatója.
A fényben úszó rajzolótermektől a későbbi gyártás szimulálására alkalmas berendezésekig (van itt esztergagép, 3D-nyomtató és fényezőkamra is) minden a tervezők rendelkezésére áll. És még valami: egy olyan virtuális valóságú szimulációs tér, ahol a világ bármely pontjáról becsatlakozhatnak a közös munkába a munkatársak.
Míg a nagy múltú, konzervatív szemléletű autógyártók rendszerint elkülönítik egymástól a műszaki és formai fejlesztést, a Daciánál közös légtérben dolgoznak a mérnökök és a tervezők, így hatékonyabb és gyorsabb (valamint szórakoztatóbb) a munkavégzés, az esetleges problémák villámgyorsan azonosíthatók és semlegesíthetők.
A fényben úszó rajzolótermektől a későbbi gyártás szimulálására alkalmas berendezésekig (van itt esztergagép, 3D-nyomtató és fényezőkamra is) minden a tervezők rendelkezésére áll. És még valami: egy olyan virtuális valóságú szimulációs tér, ahol a világ bármely pontjáról becsatlakozhatnak a közös munkába a munkatársak.
Míg a nagy múltú, konzervatív szemléletű autógyártók rendszerint elkülönítik egymástól a műszaki és formai fejlesztést, a Daciánál közös légtérben dolgoznak a mérnökök és a tervezők, így hatékonyabb és gyorsabb (valamint szórakoztatóbb) a munkavégzés, az esetleges problémák villámgyorsan azonosíthatók és semlegesíthetők.
Az elkészült tervekből először virtuális modellt hoznak létre. Ehhez rendkívül nagy teljesítményű számítógépeket alkalmaznak: a Jogger digitális makettje például 32 ezer képpontból áll, és 9 GB-nyi adatot tartalmaz. Ezen a modellen finomítják a terveket. Változtatnak a színeken, az anyagok felületén, de akár a méreteken is: így derült ki például a Jogger fejlesztésének a korai fázisában, hogy az első ajtók nem megfelelően illeszkednek – a problémát még azelőtt orvosolták, hogy legyártották volna az első fizikai modellt.
A kétdimenziós digitális makett 50 kilométerrel odébb, a Dacia frissen felépített, ultramodern tesztközpontjában ölt testet. Először virtuálisan: a CAVE szimulációs szoba háromdimenziós modellt hoz létre az adathalmazból; tíz nagy felbontású kamera vetíti ki egy kocka alakú terem falaira a megfelelően módosított képeket, amelyekből egy speciális 3D-s szemüveg használatával tökéletesen élethű, térbeli képet kapnak a tervezés alatt álló autóról.
A kétdimenziós digitális makett 50 kilométerrel odébb, a Dacia frissen felépített, ultramodern tesztközpontjában ölt testet. Először virtuálisan: a CAVE szimulációs szoba háromdimenziós modellt hoz létre az adathalmazból; tíz nagy felbontású kamera vetíti ki egy kocka alakú terem falaira a megfelelően módosított képeket, amelyekből egy speciális 3D-s szemüveg használatával tökéletesen élethű, térbeli képet kapnak a tervezés alatt álló autóról.
Itt már potenciális ügyfelekből verbuvált fókuszcsoportokat is bevonnak a további fejlesztésbe: a Jogger esetében például az itt kapott, korai visszajelzések alapján költöztették 20 mm-rel előrébb a hátsó üléseket. A két helyszínen zajló digitális szimulációkkal rengeteg időt és pénzt – évente akár kétmillió eurót – takarítanak meg, ami közvetlenül és áttételesen is segít alacsonyan tartani az autó vételárát.
A titui tesztközpontban persze nem csak virtuális vizsgálatok folynak: több mint 30 kilométernyi, változatosan burkolt tesztpálya szolgál arra, hogy a megépített prototípusokon ellenőrizzék azok zaj- és rezgéscsillapítását, a hajtáslánc és a futómű megfelelő működését. Itt két-három hónap alatt szimulálnak ötévnyi használatot; a felgyorsított igénybevétel során válogatott kínzásoknak vetik alá az autókat. A helyszín büszkesége például a porcsatorna, ahol tetszőleges szemcseméretű homokkal bombázzák alulról az autókat, hiszen a világ negyvennégy piacán eltérő körülmények között kell helytállniuk, akár olyan helyeken is, ahol a földút jellemzőbb, mint az aszfaltozott.
A legváltozatosabb magasságú és szerkezetű járdaszegélyekre állnak itt fel, és ugratnak le azokról naphosszat, édes- és tengervizes pocsolyákon hajtanak át. A teljes sebességtartományban vizsgálják az illesztések pontosságát, az autó viselkedését, a szél- és útzaj mértékét és jellegét.
A legváltozatosabb magasságú és szerkezetű járdaszegélyekre állnak itt fel, és ugratnak le azokról naphosszat, édes- és tengervizes pocsolyákon hajtanak át. A teljes sebességtartományban vizsgálják az illesztések pontosságát, az autó viselkedését, a szél- és útzaj mértékét és jellegét.
Ha az első két helyszínen jelesre vizsgázott egy új modell, elérkezik a harmadik, végső fázishoz, a gyártáshoz. Ez Európában a Dacia hagyományos helyszínén, Mioveniben zajlik, ám az elmúlt tizennyolc évben Észak-Afrikában, valamint Kínában is létesített gyártóbázist a márka.
A mioveni présüzem naponta 900 tonna acéllemezt alakít át csaknem 300 ezer egyedi nyers alkatrésszé; ezek egy részét más gyárakba szállítják, a maradék pedig a 46 százalékban robotizált karosszérialakatos műhelyekben nyeri el végső formáját. Könnyű felismerni azokat a munkafázisokat, amelyeket robotok végeznek, hiszen a csarnok ezen szakaszain világítás nélkül zajlik a munka – ezzel megint csak jelentős energiát és pénzt takarít meg a Dacia.
A mioveni présüzem naponta 900 tonna acéllemezt alakít át csaknem 300 ezer egyedi nyers alkatrésszé; ezek egy részét más gyárakba szállítják, a maradék pedig a 46 százalékban robotizált karosszérialakatos műhelyekben nyeri el végső formáját. Könnyű felismerni azokat a munkafázisokat, amelyeket robotok végeznek, hiszen a csarnok ezen szakaszain világítás nélkül zajlik a munka – ezzel megint csak jelentős energiát és pénzt takarít meg a Dacia.
A végső összeszerelésben naponta 1400 – évente 350 ezer – autó készül el, méghozzá a lehető legegyszerűbb és legmegbízhatóbb módon. Számos autógyár kifinomult, kameraalapú pozicionáló rendszert alkalmaz a karosszéria és a hajtáslánc összeillesztése során. Mioveniben ellenben a gravitációra, a hajszálpontos méretezésre bízzák a feladatot – ez kevésbé látványos, viszont tökéletesen működik, és a szenzorrendszer hiánya miatt kisebb a meghibásodás lehetősége is.
Ez utóbbi tökéletes végszó a történethez, hiszen pontosan egybevág a Dacia filozófiájával: ahelyett, hogy túlbonyolítanánk a dolgokat, a lényegre kell törekedni, azt viszont tökéletesen kell megvalósítani.
Ez utóbbi tökéletes végszó a történethez, hiszen pontosan egybevág a Dacia filozófiájával: ahelyett, hogy túlbonyolítanánk a dolgokat, a lényegre kell törekedni, azt viszont tökéletesen kell megvalósítani.
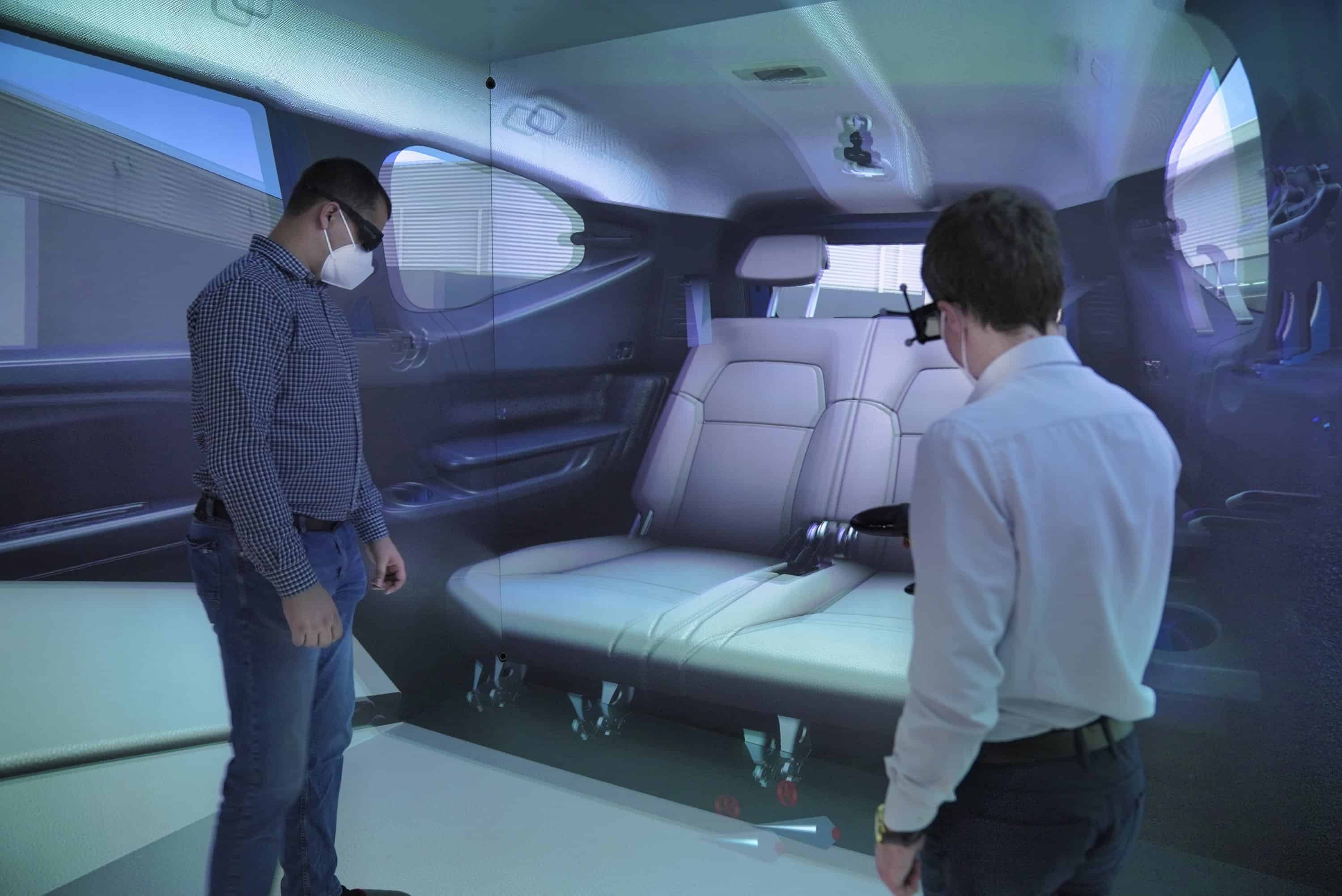
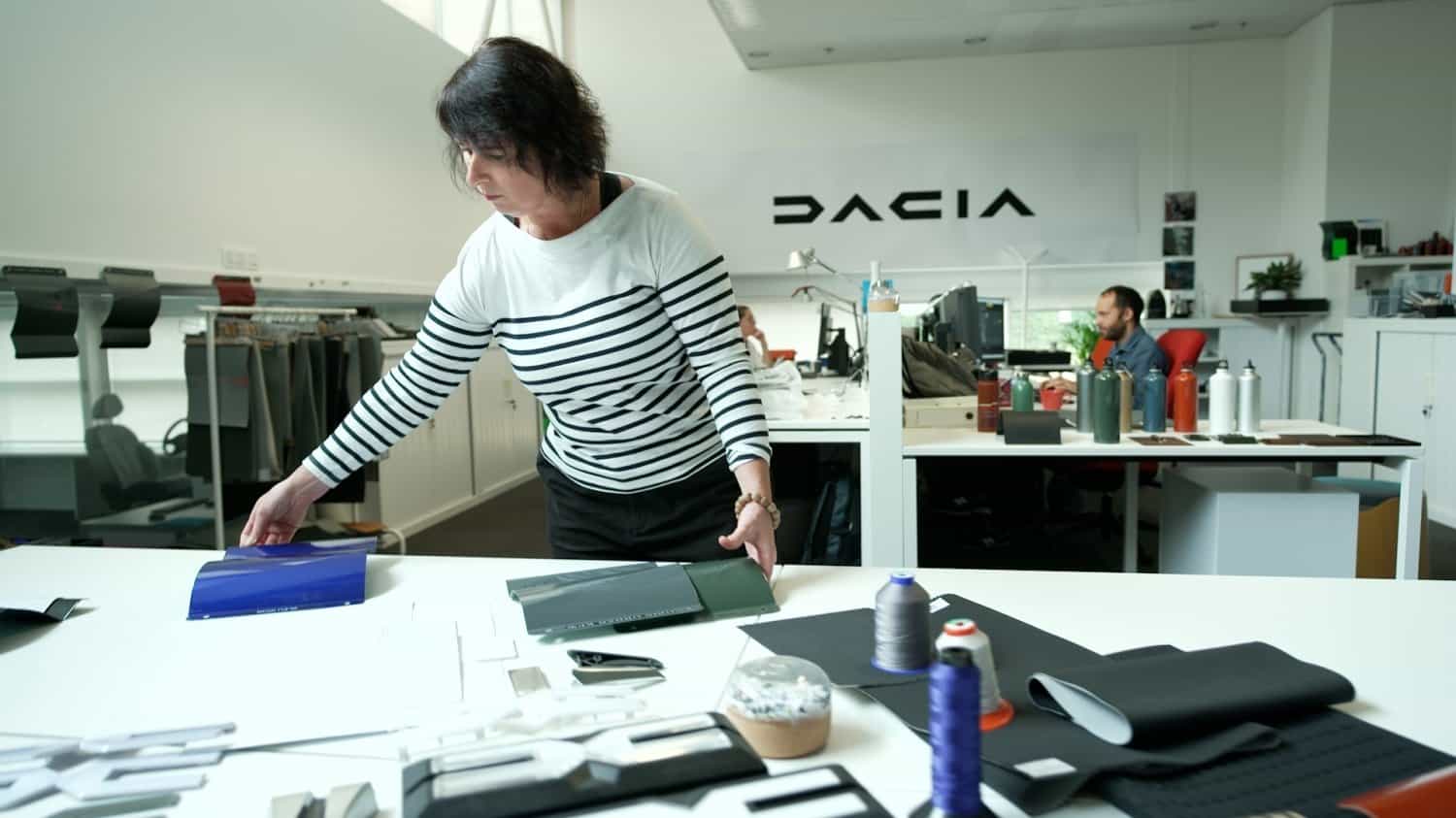
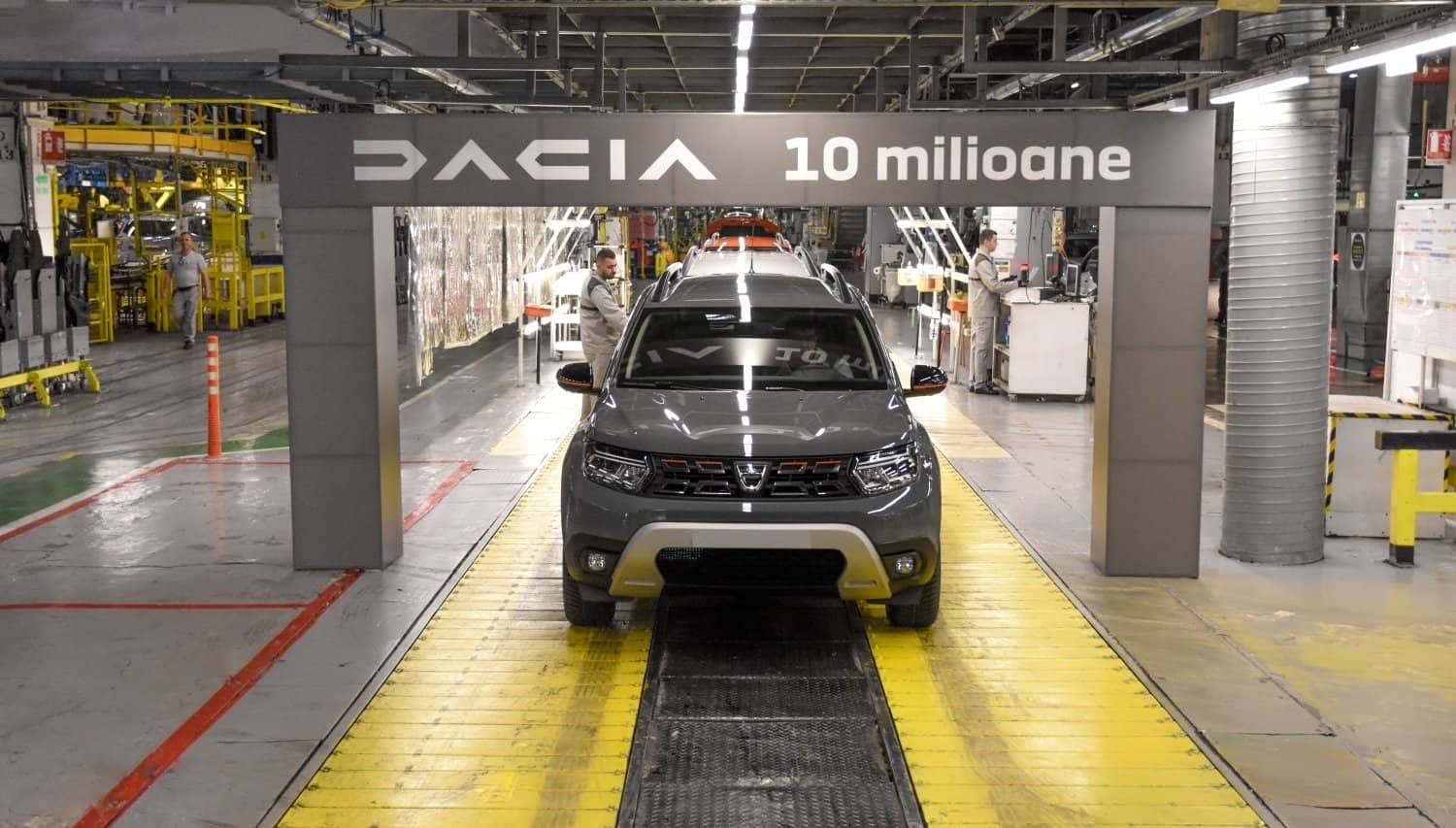
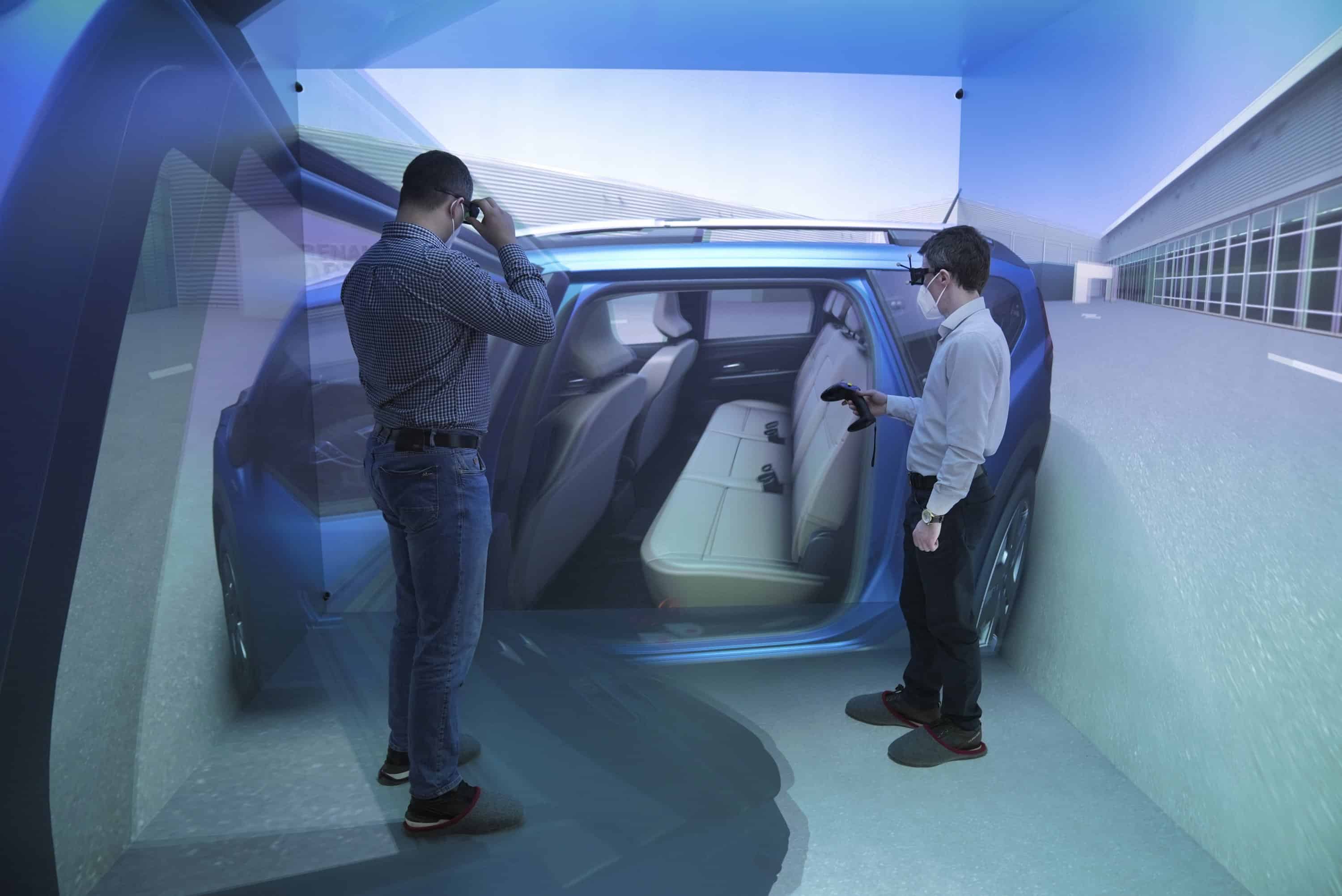
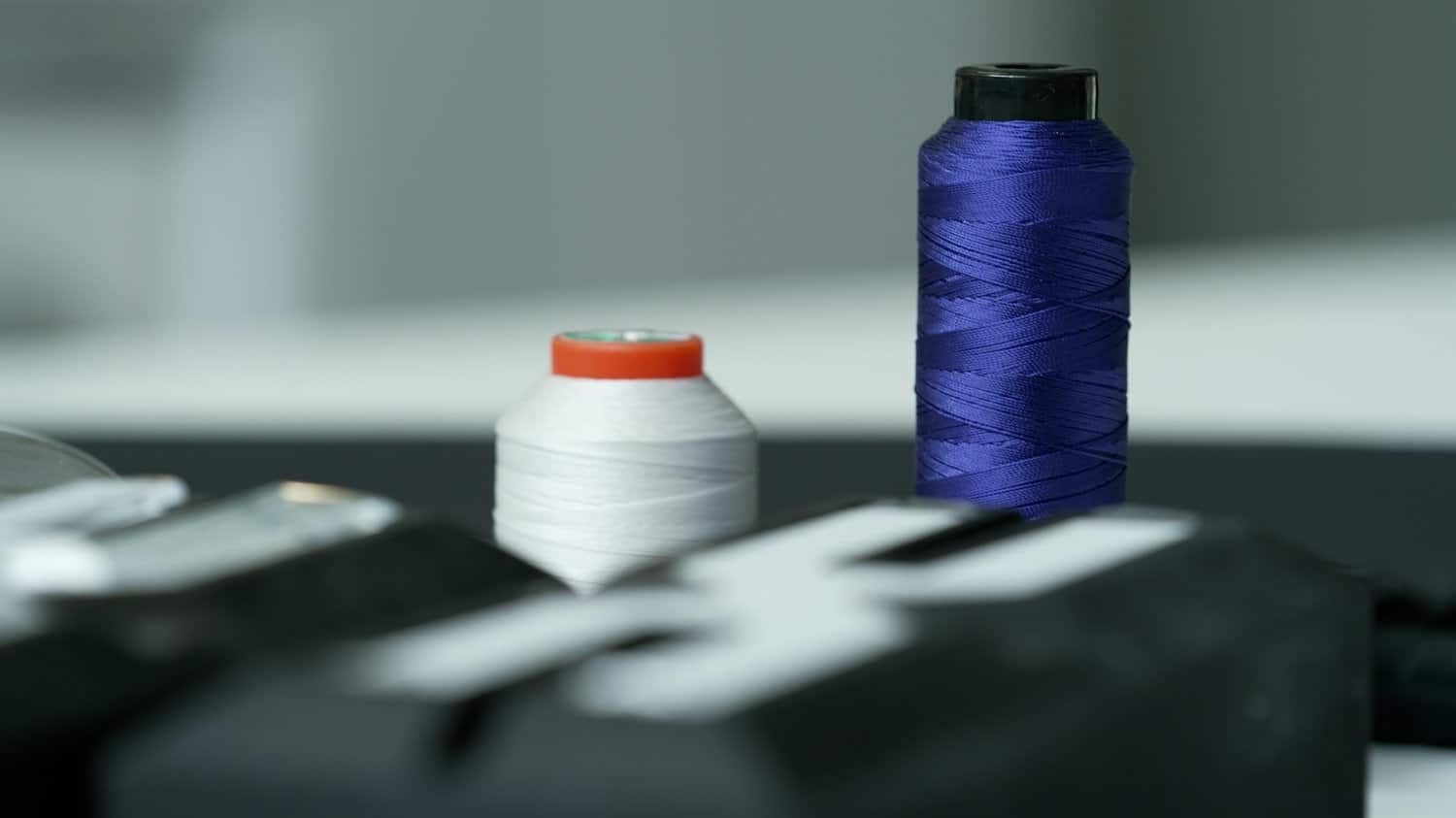